Material Driven Design
In this post I have documented and discussed my experiment with pine resin as part of the Material Driven Design course.
A brief history of resin
Plant resin is mostly composed of terpenes and is considered to be a volatile substance. Apparently, our ancestors used a mix of resin and ashes to create a ‘glue stick’ which was an indispensable part of every hunter gatherer’s toolkit (belt kit to be more precise). They used it as a fire starter, to quickly glue arrow heads and other tools. This finding is based on anecdotal evidence from survivalist how-to videos on YouTube, but it sounded sensible enough not to require further investigation.
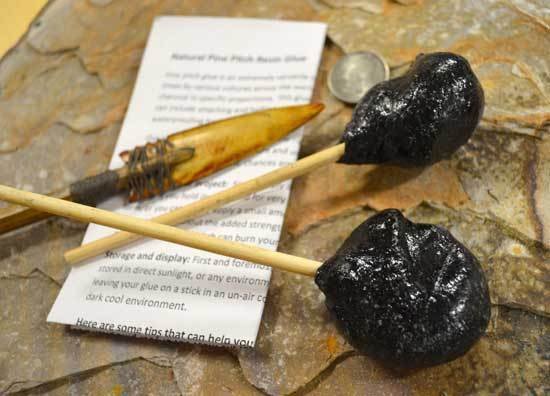
A quick Wikipedia search corroborates the historical use of resin as an adhesive for hafting stone tools. Ancient Egyptians and Greeks used resin for therapeutic purposes, food and incense. Today resin is used to produce varnishes, adhesives, food glazings, incense and perfumes.
Resin picking
I collected the first batch of resin in an afternoon hike to the Green Fab Lab in Valldaura and back. At the beginning I had hard time finding the right trees and spotting resin on them. But with each examined tree I was getting better at tacitly recognizing which ones have a higher chance of having resin leaking from them and to discern at distance resin covered in debris from bark of the tree.
Curiously enough, it wasn’t the largest holes and scars that accumulated the most resin in them. It was often rather small openings or seemingly undamaged surfaces that were the most potent source. It is worth noting, that the process of collecting was quite tedious, as you have to repeatedly scrape the tree and fiddle your knife in small gaps to obtain what amounts to resin dust. On a few lucky occasions I was able to pick larger solid chunks.
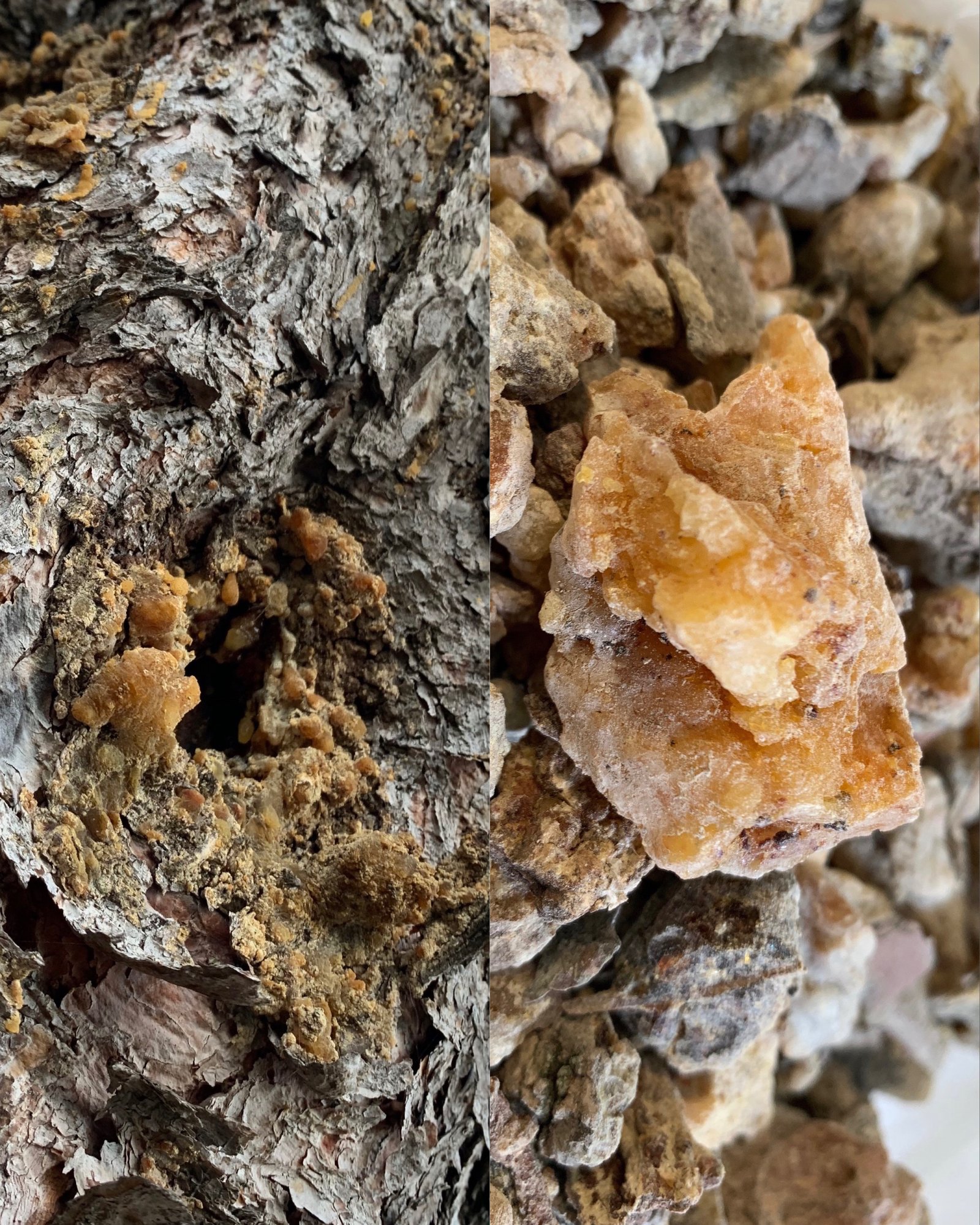
It was particularly interesting to see the different properties of the material depending on the age and tree it was picked from. Fresh resin had a clear translucent color and was too sticky and runny to be picked, while older resin was significantly darker, dry, solid and covered in debris, making it difficult to spot, but quite easy to pick. It also seemed that different trees produce differently colored resin. Since I only noticed this after the fact, I was not able to observe which tree produces certain types of resin.
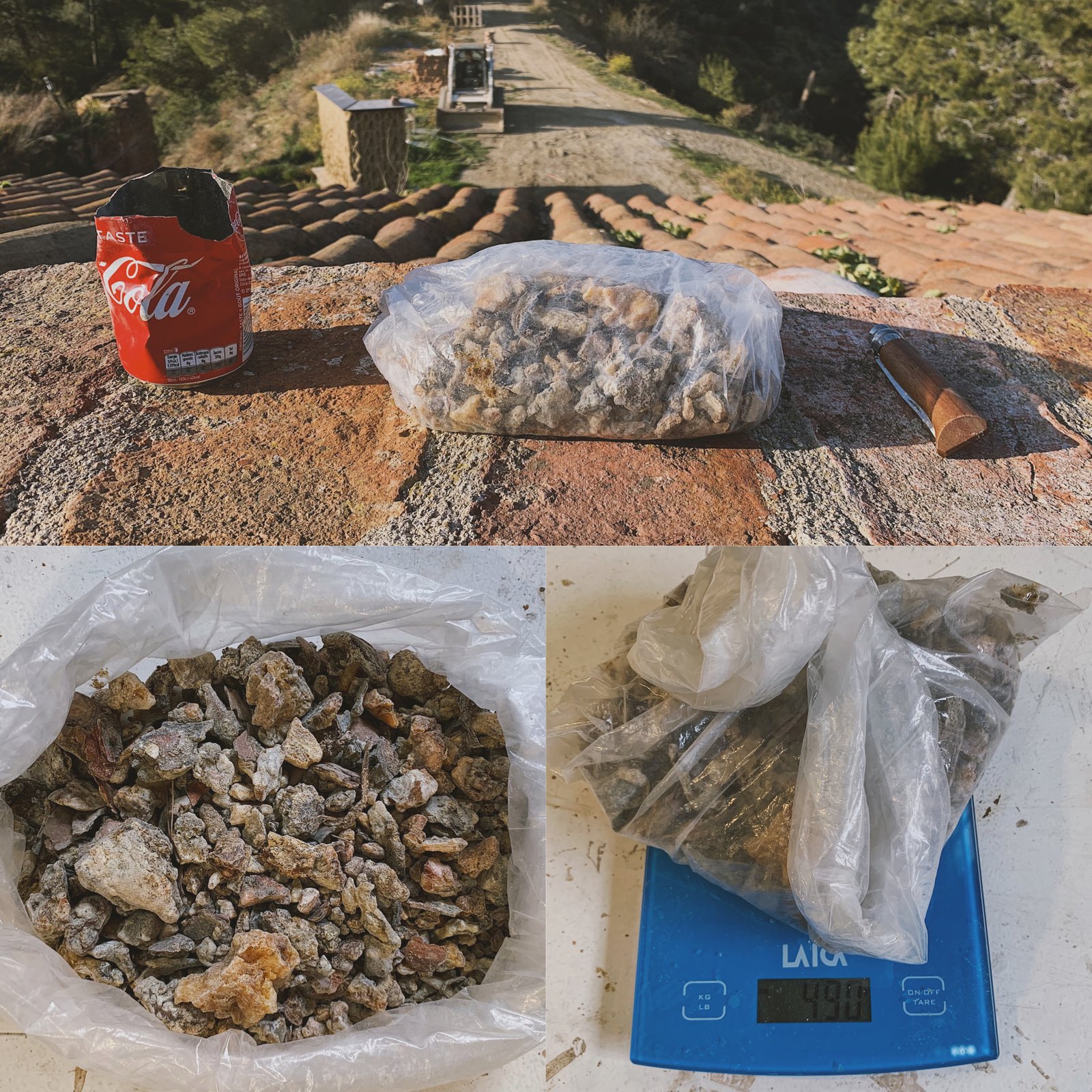
On a more personal note, going out in the woods to collect resin turned out to be a deeply enjoyable and meditative experience. As I was getting more immersed in the whole process I started talking to the trees – apologizing for poking them with my tiny knife, thanking them for their resin, commenting on the surroundings and sometimes just talking about whatever crossed my mind at that moment. At first, I was taken aback by my actions but I quickly accepted it as part of the learning. This behavior that would likely be considered out of the social norm in an urban context felt completely natural, acceptable and even encouraged in the forest context. Despite being the only specimen of homo sapiens in the vicinity, I did not feel alone.
As the day progressed I felt my senses heighten and get more attuned to the subtle rhythms of the Valdaura forest which resulted in my increased ability to spot and collect resin. Insights gained from this experience were a great example of the value of embodied learning as well as being highly relevant to my final project which focuses on non-human intelligence and improving our connection to other living organisms.
ResinLab™
Before I started experimenting, I have selected and put together all the tools and containers that I would need throughout the process. Main reason being that resin is extremely difficult to scrape off and clean so I assumed that everything I used is going to be only good for another resin experiments in the future.
The first step in my material experimentation was to heat up all the collected resin and filter out the impurities, or at least get rid of the larger pieces of debris. I have used a rudimentary DIY strainer made from a mesh. This method worked quite well initially, but since the resin is quite dense and starts solidifying almost immediately after being poured, I had to wait for the resin that got stuck on the strainer to cool down, scrape it off, reheat it and pour it again. I had to repeat this process several times, but I managed to a significantly cleaner-looking resin mix.
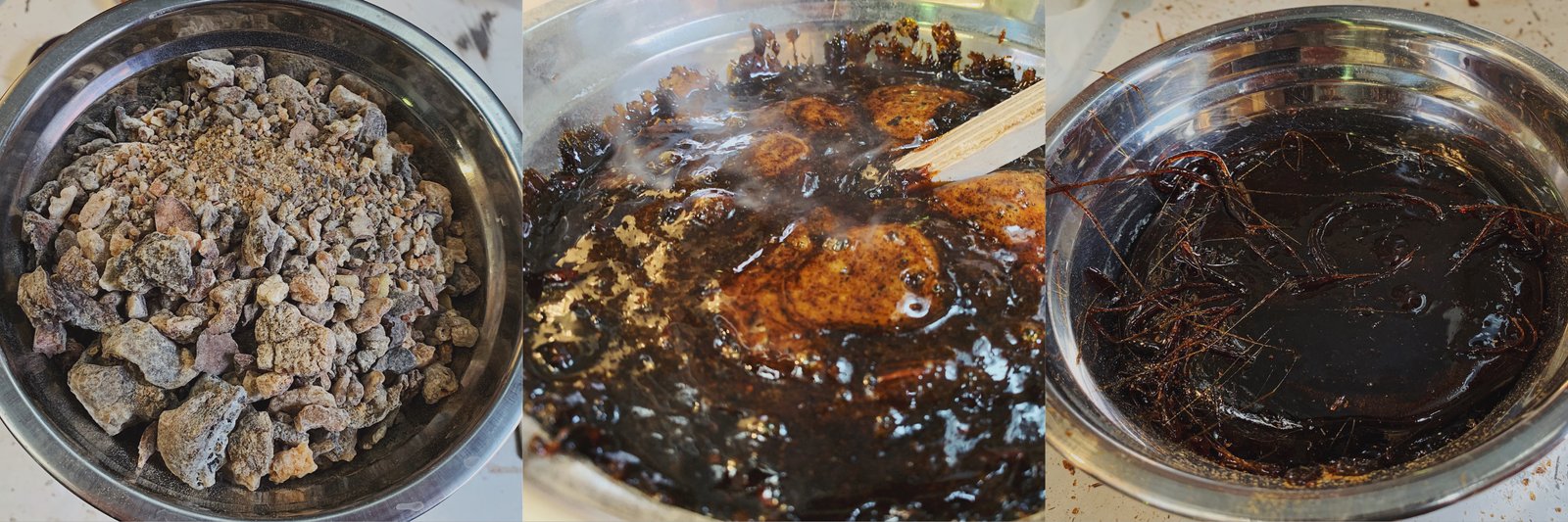
Each time I have gone through a cycle of heating up the resin and then waiting for it to cool down its properties changed slightly – color was turning darker, the hot resin was becoming more liquid and the solidified substance seemed overall less sticky and more brittle. This was an important finding because I now know that I need to better prepare and organize the experiments in the future so I can minimize the number of cool down cycles.
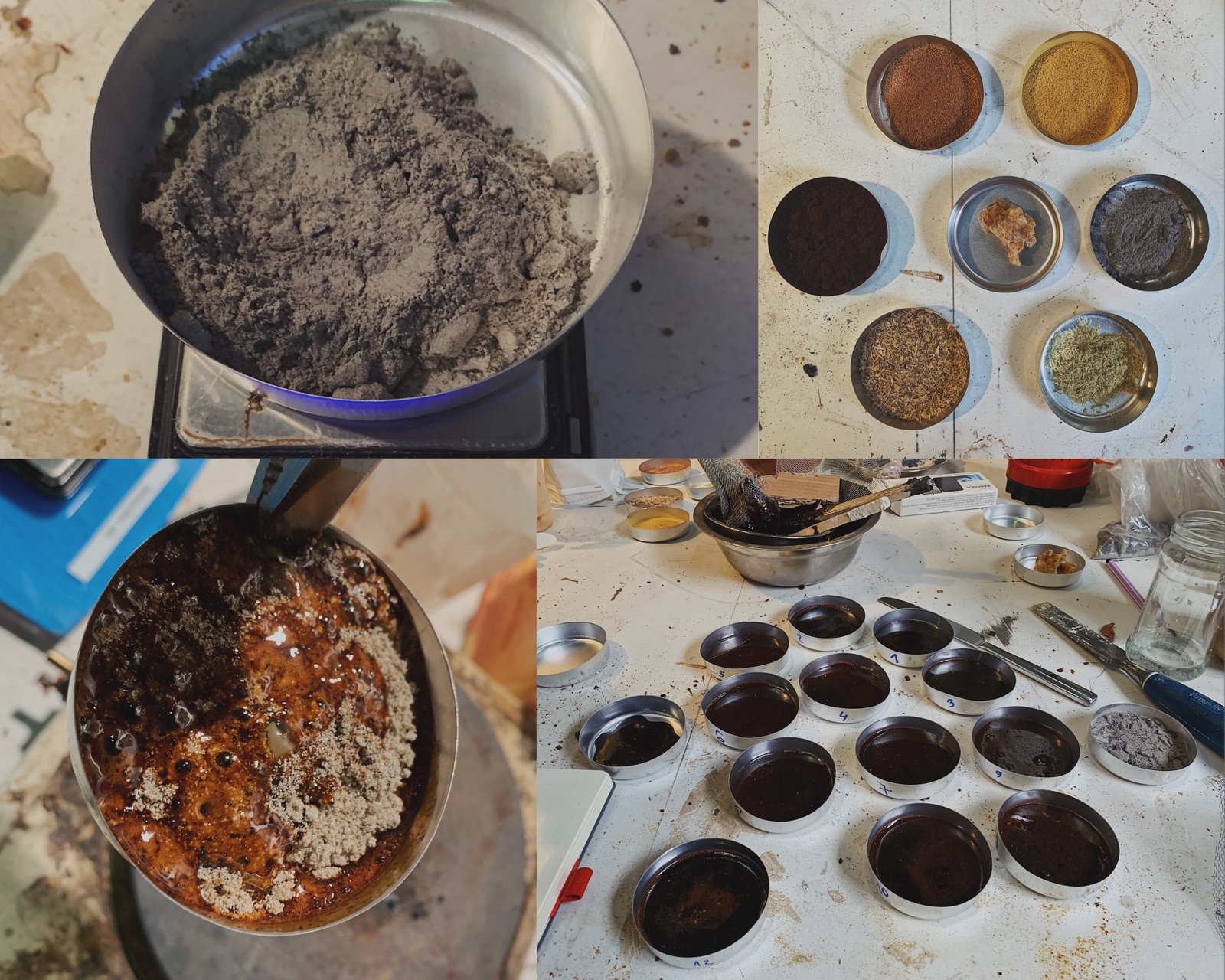
I decided to perform a sort of a meta experiment by using powdered materials that my colleagues have created as part of their respective experiments. Besides those, I have also mixed the resin with ash, since that was how adhesive was made in pre-historic times. The resulting mixtures all had similar properties. The most flexible mixture seemed to be based on silica.
Following is a summary of the various resin mixtures:
sample | resin | addition | comments |
---|---|---|---|
1 | 20,68 g | 5,02 g coal ash | |
2 | 20,98 g | 10,02 g coal ash | |
3 | 22,58 g | 15 g coal ash | |
4 | 20,7 g | 10,10 g used coffee grounds | |
5 | 21,17 g | 6,52 g powdered orange peel | beutiful colors and aromas |
6 | 20,22 g | 1,63 g powdered palm lignin | |
7 | 21,36 g | 1 g powdered bamboo fiber | quick absorption |
8 | 21,22 g | 9,02 g powdered bone calcium | rapid and intense reaction |
9 | 21,82 g | 2,1 g silica | slow absorbption, intense initial reaction |
10 | 21 g | 4,09 spent grain |
Presintation
As I was experimenting I quickly became fond of the aesthetic and surface finish of the different mixtures that took a shape of the small aluminum forms that I have used . Therefore, for the purposes of presenting the results, I decided to laser cut a simple tray that fit the rounded samples along with a compartment for raw resin samples.
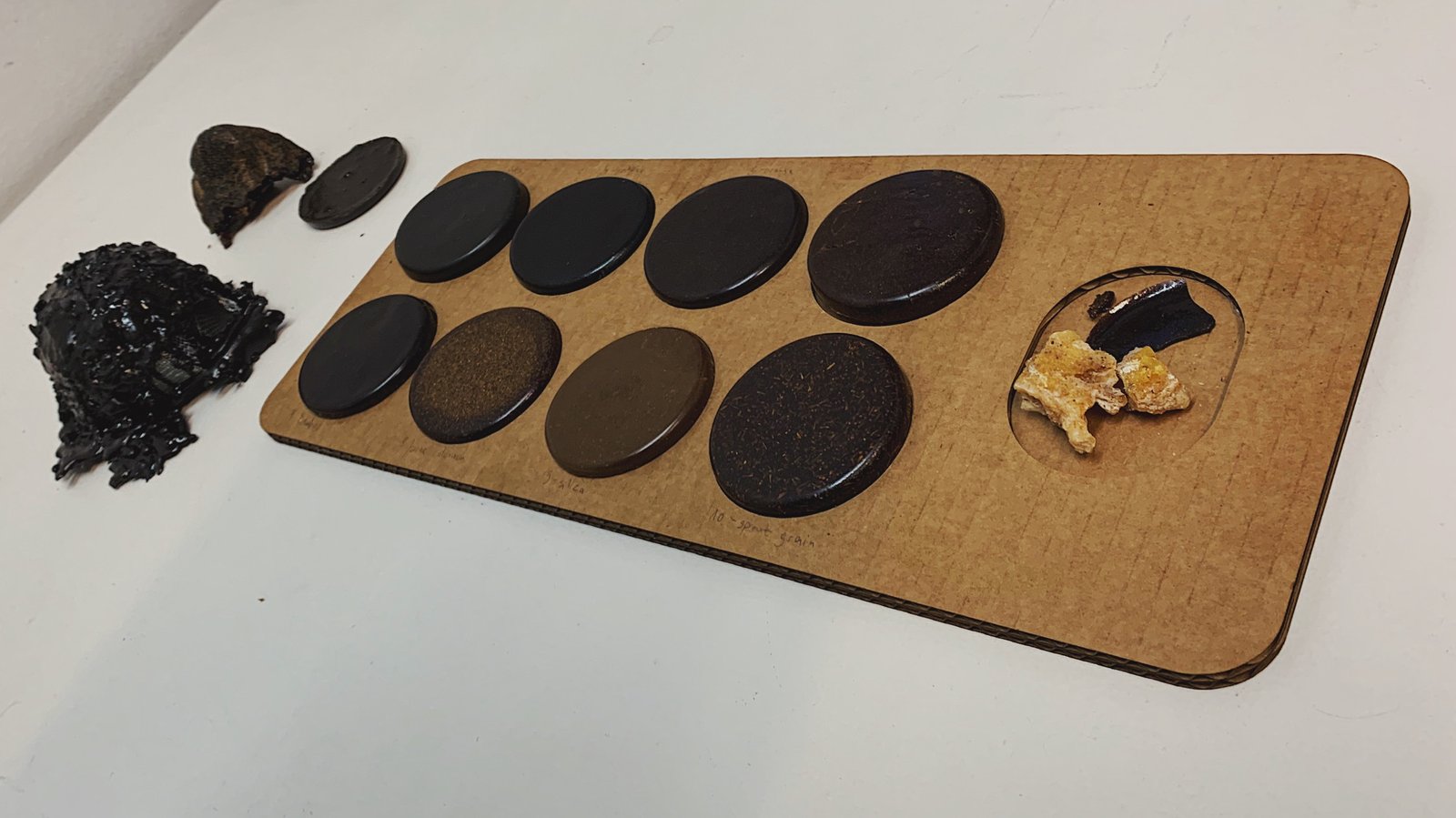
I mixed the remaining resin with ash and poured the mixture in a primitive mold. However, due to my lack of knowledge on how to properly make molds, my initial attempt to create a solid object failed. Also, I have used too much Vaseline, which resulted in a rather sticky substance that I have re-purposed to form a sort of a blob. Although accidental, the final Vaseline-infused substance was very flexible, resulting in well-performing material.
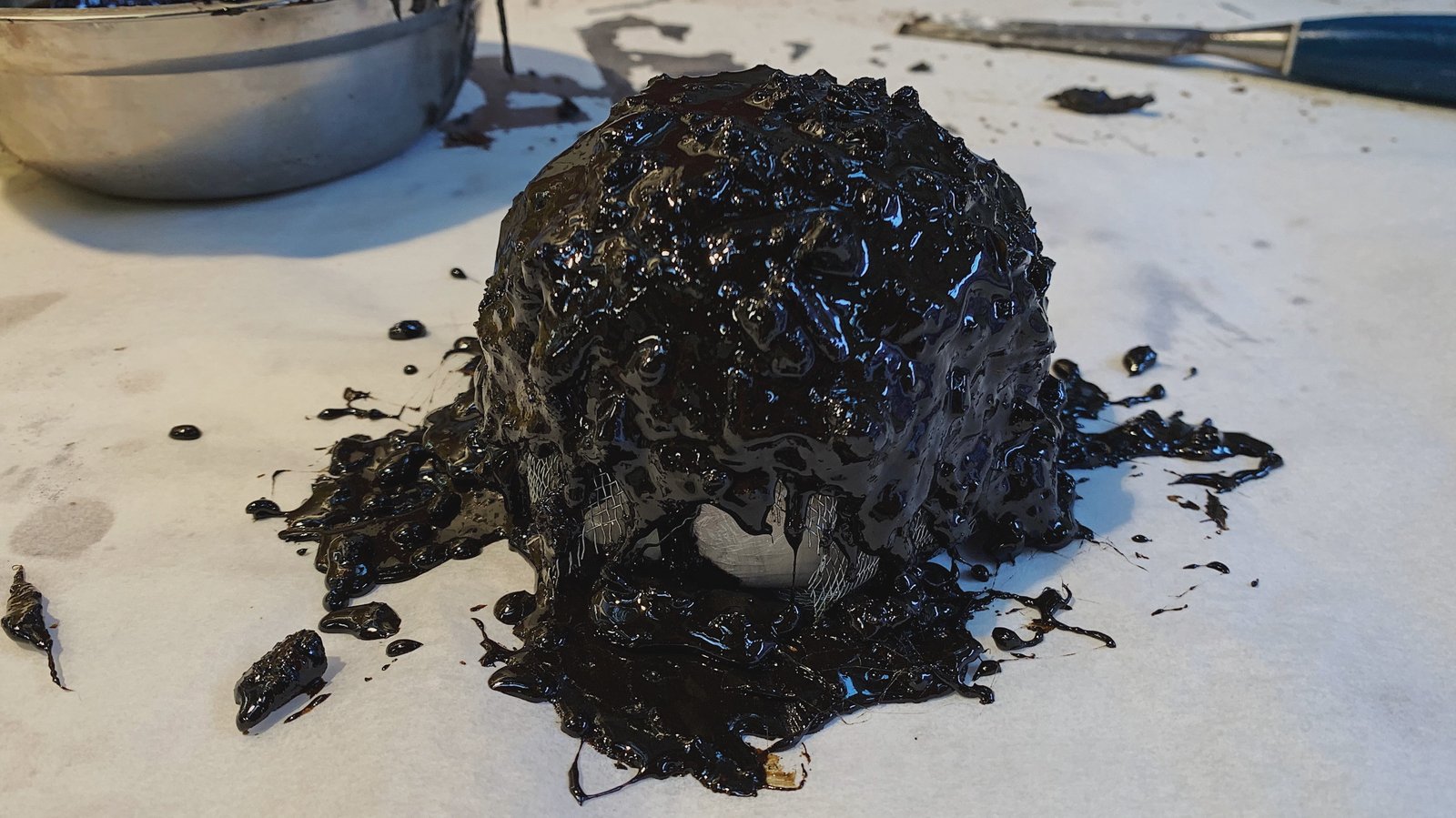
The resin futures
Due to time constraints and limited availability of hand-picked resin I was not able to push the limits of my chosen material. In the process of experimenting and presenting the initial outcomes I have gained new knowledge that will affect my future work with this material. First, I would like to try a better method for purifying the resin and filtering out the debris in order to obtain a more clear base material. Secondly, I would like to mix the resin with a more viscous substance to create a less brittle and more malleable material. For that purpose, I will focus on wax, ideally bees wax, which neatly complements the resin due to its natural origin.
I would love to incorporate resin as one of the materials in my final project due to its function as a protective agent for trees.